How to Setup a Fluid Dynamics Analysis (CFD)
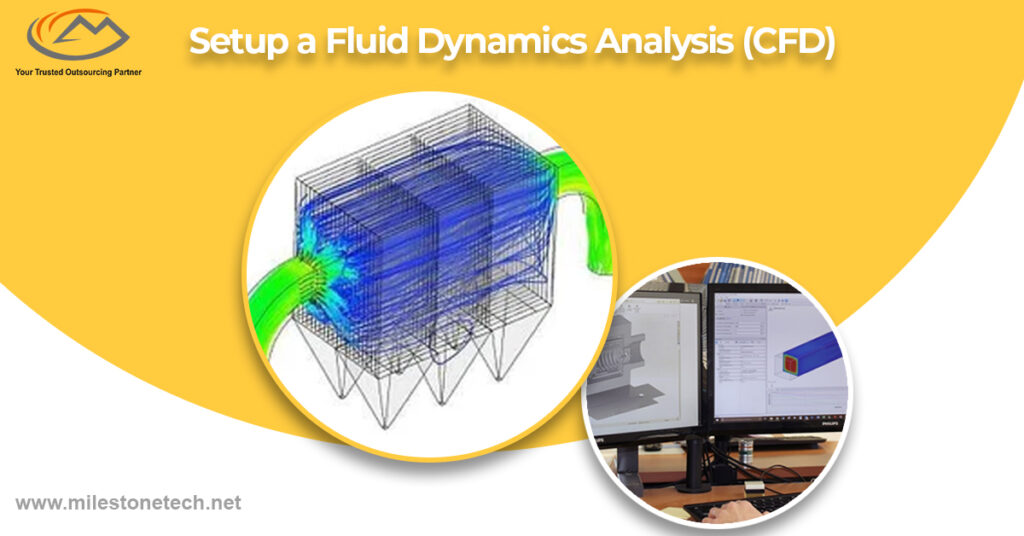
Computational Fluid Dynamics Analysis is a process of rearranging different systems and processes in a digital environment. With this system, there is a lot of pre-process and post-processing options. The system can be used for water flow, calculating the strength of liquid. It has provided scientists with a more powerful tool to replace traditional methods. Using Computational Fluid Dynamics, you can create simulations that are comparable to the ones created in a lab. This method is based on the following fluid forces:.
⭐ Newtons second law
⭐ Mass conservation
⭐ Energy conservation
Flow and pressure is an issue in design, which can be tackled through the use of computational fluid dynamics to analyze the resultant data. This method takes care of problems that designers would not have been able to solve on their own, bringing them a safer and more comfortable environment. It is used to control the aerodynamic features of aircraft and reduce health risks by simulating walking on cars. This technology is increasingly being used to forecast pressure fields and is able to estimate the interference caused by helicopters.
With careful modeling and settings for imitation, we can obtain a successful analysis. The geometry of CFD Services is well-designed and it’s easy to get an understanding of what the desired effects are. To trust the results of any simulation, you need accurate measurements, modeling, and a description of how the simulation should function. The performance of CFD simulations depend on the user’s valid input, so if there is an inaccurate instruction in the software, it will produce unexpected results.
In order to create a CAD model that is useful in your Computational Fluid Dynamics Analysis, you’ll first need to know whether you are looking at internal or external flow. For the internal flow, a standard object can be modeled in 3D CAD software. If external flow around a non-physical object is a consideration, then the model can re-enter into In order to accurately create a simulation, you will need to first consider the shape of the object in the fluid (large or small) as well as fluids in and around the object. You can also create objects inside your CAD software through large boxes and then import them into your simulation software simulation CFD.
Details will be shown in a Computational Fluid Dynamics Analysis, but it is important to not make the models too complicated with small details because it will take more time and won’t change the results. Simplification is important, but not so much simplification that it leaves out the important details in the model that affect water flow. The first step in CFD mesh creation is usually with automated machine distribution. Mesh refining is exactly the same as FEA and can be treated the same way by using their built-in filter tool
If a mesh is too rough, the imitation will not have accurate results. On the other hand, a very good mesh cannot always extract important information from the simulation in order to achieve the best design solution. One solution is adapting meshing, which filters meshes according to repetitive effects of a simulation. The application of simulation and compressive sensing here, which occurs many times to show different outcomes, makes certain locations relevant in the match. When it comes to the junction between the mesh and solution junction, we should note their differences discussed in more detail in the resolution phase. For flexible meshing to be more efficient, a quality first mesh must be created.
The first step in a Computational Fluid Dynamics Analysis engineering challenge is to refine the CAD geometry. At this stage, the engineer identifies unnecessary elements such as ties, anchors, or small details and removes them from the model. They also clean up any spaces or holes in the model that may be problematic for a CFD solution. The quality of the CFD simulation is determined by the CAD geometry that is inputted. Low Computational Fluid Dynamics simulations limit the predictive quality and cause engineers to use limits on negative geometry when creating computer models. With GIS software, engineers can incorporate circuit physics into their schematic models. It is not required for the model to be fully representative of real world physics parameters.
Using a mesh, an engineer can create a CFD simulation. The cells in the meshes make up many small parts of the geometry, and by using structured physics, you can solve for it. But not all meshes are equal; some imitation hinges can wreak havoc on the simulated problem. Mesh sizing is one of the most crucial steps in a CFD engineer’s work process. The number of potential problems are:
⭐ Physics settings are incorrect
⭐ Additional match fixes are required for problematic area
⭐ Imitation of instability
⭐ Bad results
⭐ Some unknown problems
There are many ways to test if a product is original or fake. One way is by using an independent mesh study which evaluates imitations and through the use of simulations to predict the accuracy of a match. When there is no change in the simulation no matter how large or small the imitation, then the engineer can conclude that they have found an accurate match. The next step involves defining a solved parameters, such as solver parameters and discretization schemes. Depending on what type of simulation you’ve chosen, each problem has its own unique structure. It’s important to find appropriate solver parameters and number systems for solving the problem successfull
Product designers are constantly on the move as new methods and processes change the way they design. Innovators attempt to meet new challenges that face product designers every day by using newer methods.
Configuring the design process can speed up other processes. If you find that the design is constantly being updated, there are likely other processes that have slowed down – like not including the structural inputs.
The design process can be complex and the product may be too overused. Both the manufacturing process and the product can lead to potential business problems.
Customer Involvement – The customer can provide input about the design process, which is helpful for designers. But to get more productive feedback, some focused questions are needed.
Sustainability is an issue for many designers, especially if the product is not economically or environmentally friendly. A designer may have a great idea for a new design, but it can prove too expensive to produce.
Follow Milestone PLM Solutions for Mechanical Industry Updates, CAD Tips and Global CAD, CAM & FEA News.
Milestone PLM Solutions with its exclusive delivery center in India is a global CAD, CAM & FEA services outsourcing partner serving the needs of the Mechanical, Millwork and Automotive industry since 2004. MILESTONE focuses on the unique needs of clients and believe in tackling real-life problems with efficiency, smooth and ease.
The MILESTONE team can assist you with Product Design, 3d Modeling, Drafting & detailing, Reverse Engineering, FEA Analysis and more. We support multiple software including AutoCAD, Solidworks, Catia, NX, Inventor, Solidedge & Ansys etc. Our approach is to provide a dedicated team for each customer over ongoing project and deliver the quality output consistently.
With our state of art technology and large talent pool of Engineers, we are developing best in class solutions for our customers across the globe. We align with your culture and values to form unbreakable partnerships and are primed for success with over 100 employees and 150 customers in the US, Europe, India, and Asia.
For more queries regarding any of the above-mentioned topics, feel free to connect with us on our website www.milestonetech.net or contact us on +1-844-598-0005