Top Benefits of Process Simulation in Manufacturing and Beyond
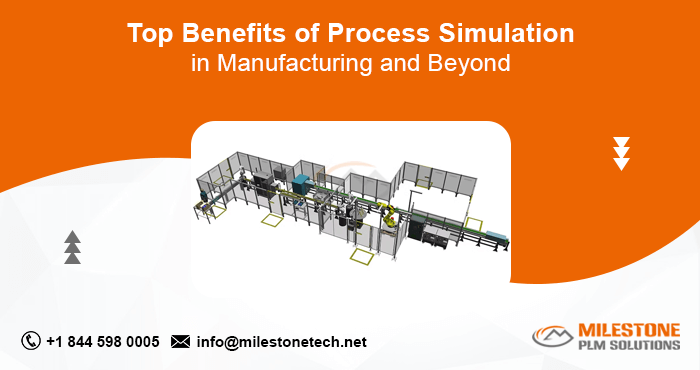
With the growing demand of the fast-paced industrial environment today, efficiency and precision are more important than before. Whether it is in manufacturing, logistics, or even healthcare, companies are under growing pressure to optimize the processes that build their products, reduce costs, and retain competitive advantage. Process simulation is one of the best tools to achieve these goals. The approach offers companies a way of analyzing, predicting and improving the performance of such processes by creating virtual models of real-world operations that do not involve the costs and risks of trial-and-error in real-world settings.
What is Process Simulation?
Process simulation refers to the simulation of a certain physical process by means of specialized software. In fact, the model itself is built to simulate the real-world working of the process in different scenarios. By simulating these scenarios, organizations are able to:
- Test different configurations.
- Identify bottlenecks.
- Predict outcomes based on specific inputs.
Process simulation ensures that whether it is a production line, a supply chain network, or a complex chemical reaction, the decision-making is done in an informed manner to achieve optimized efficiency and, as a result, cost-effectiveness.
Top Benefits of Process Simulations
Enhanced Process Efficiency
With process simulations, one of the sharpest gains within reach is the ability to identify inefficiencies across manufacturing-related workflows. Manufacturers can identify problem areas and streamline workflow through simulation of multiple scenarios. A car manufacturer, for instance, can simulate its assembly line processes, analyze it, and thus determine the best combination of machinery and workforce layout that minimizes production time and cost.
Cost Savings
It can be expensive and time-consuming to build and test physical prototypes. Process simulations reduce the number of prototypes used to design an order of operations as engineers can check designs within an artificially designed environment. This not only saves money on raw materials but also decreases outside production time. Process simulations are invaluable for safety and cost-effective operations in such industries like chemical manufacturing, wherein trial and error can prove detrimental and costly
Risk Reduction
By simulating processes in a virtual environment, organizations can identify potential failures or hazards before they ever happen in the real world. This is especially valuable for high-stakes domains like aerospace, healthcare, and energy, where errors can lead to disastrous outcomes. Pharma companies, for instance, utilize process simulations to enhance drug manufacturing processes and ensure compliance with several safety and quality standards.
Improved Decision-Making
Process simulations help transform complicated data into tractable format that empowers decision makers to make actionable insights. They are able to do this by enabling data-drive decisions that enhance operational performance. Supply chain managers, for one, can play out various logistics scenarios to find out the most efficient route to deliver goods based on factors like fuel costs, traffic patterns, and delivery deadlines.
Flexibility and Scalability
Process simulations help transform complicated data into tractable format that empowers decision makers to make actionable insights. They are able to do this by enabling data-drive decisions that enhance operational performance. Supply chain managers, for one, can play out various logistics scenarios to find out the most efficient route to deliver goods based on factors like fuel costs, traffic patterns, and delivery deadlines.
Accelerated Time-to-Market
This translates into automating virtual processes and substantially decreasing the time to market for new products or services in firms. Responding quickly to market demands means faster time-to-market and thus, higher competitiveness and improved customer satisfaction. In consumer electronics, where product lifecycles are short, process simulations enable companies to iterate production steps, delivering high-quality products faster.
Sustainability and Environmental Impact
Process simulations can be a powerful enabler to help organizations achieve their sustainability targets. Businesses can uncover opportunities to minimize their environmental impact through the analysis of energy use, materials usage, and waste generation. For instance, the factory can design its processes and layout using simulation tools that will eliminate waste and optimize energy usage, resulting in cost savings and also an environmental steward.
Employee Training and Skill Development
But process simulations are not only used for improving operations, they are also used for training and skill enhancement. Virtual simulations can enable employees to practice and develop their skills with a reduced learning curve and, ultimately, a more competent workforce. For example, oil and gas industry operators can safely and effectively practice operating complex systems in a virtual environment.
Cross-Industry Applications
While process simulations are most commonly associated with manufacturing, their benefits extend far beyond. Industries such as healthcare, logistics, retail, and even urban planning are leveraging these tools to optimize their operations.
- In healthcare, process simulations help design efficient patient flow systems in hospitals, reducing wait times and improving care delivery.
- In logistics, simulations assist in optimizing warehouse layouts and transportation networks, ensuring timely deliveries and cost-effectiveness.
Real-World Examples of Process Simulations
- Automotive Industry: Automotive manufacturers use process simulations to design and optimize production lines, ensuring maximum efficiency and minimal waste. By simulating different assembly line configurations, companies like Toyota and Ford have achieved significant cost savings and improved product quality.
- Chemical Processing: In chemical manufacturing, simulations enable engineers to model reactions and test different conditions to achieve desired outputs without risking plant safety or wasting raw materials.
- Logistics and Supply Chain: Companies like Amazon use process simulations to optimize warehouse operations, from storage layouts to delivery routes, ensuring faster order fulfillment and reduced operational costs.
Conclusion:
Process simulations have several undeniable advantages. Through a risk-free platform that enables companies to test and optimise operations, these tools help companies maximise levels of efficiency, cost savings and innovative operations like never before. Across industries from manufacturing to healthcare, process simulations are changing the way organizations approach problem-solving and decision-making.
Industries are evolving, leading to the increased adoption of process simulations automating smart, more sustainable operations. Process simulation technology is a key enabler for process innovation, and in today’s dynamic business environment, investing time in this area will see dividends in the future.
Now is the time to discover what tools and technologies can turn your vision into reality if you are ready to unleash the full power of process simulations in your organization.
Manufacturing simulation enhances efficiency, reduces costs, and improves productivity by allowing businesses to test processes in a virtual environment. It identifies potential issues, optimizes resource utilization, and minimizes risks. Additionally, it accelerates decision-making and supports sustainable practices by reducing waste and energy consumption.
Process simulation is essential for analyzing and improving workflows. It enables manufacturers to visualize processes, test scenarios, and evaluate performance before implementation. This leads to informed decision-making, cost savings, and enhanced operational efficiency while ensuring scalability and adaptability to changing market demands.
Simulation in manufacturing is most beneficial for process optimization, production planning, and resource management. It helps in analyzing complex systems, testing new designs, and predicting outcomes without disrupting actual operations. It’s crucial for identifying bottlenecks, reducing downtime, and ensuring high-quality output.
Follow Milestone PLM Solutions for Mechanical Industry Updates, CAD Tips and Global Mechanical News.
Milestone PLM Solutions with its exclusive delivery center in India is a global CAD, CAM & FEA services outsourcing partner serving the needs of the Mechanical, Millwork and Automotive industry since 2004. MILESTONE focuses on the unique needs of clients and believes in tackling real-life problems with efficiency, smooth and ease.
The MILESTONE team can assist you with Product Design, 3d Modeling, Drafting & detailing, Reverse Engineering, FEA Analysis and more. We support multiple software including AutoCAD, SolidWorks, Catia, NX, Inventor, Solidedge & Ansys etc. Our approach is to provide a dedicated team for each customer over ongoing project and deliver the quality output consistently.
With our state of art technology and large talent pool of Engineers, we are developing best in class solutions for our customers across the globe. We align with your culture and values to form unbreakable partnerships and are primed for success with over 100 employees and 150 customers in the US, Europe, India, and Asia.
You can email us at info@milestonetech.net and can log in to our website www. milestonetech.net to know more about our services and our work portfolio or contact us on +1-844-598-0005