How FEA and CFD Complement Each Other in Engineering Design
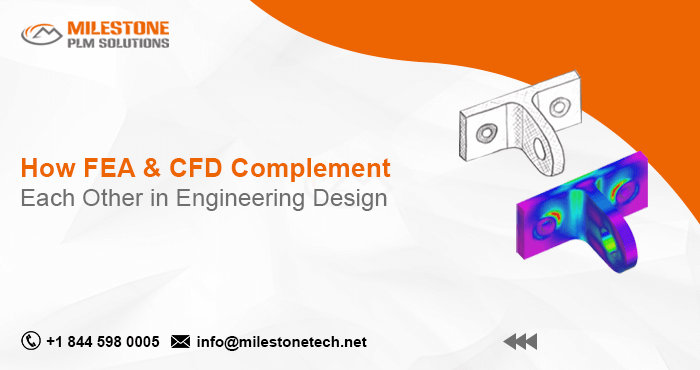
Simulation Technologies: Revolutionizing Engineering Design with Virtual Reality and AI Within the industry, two of the most powerful tools used in simulating physical phenomena and optimizing designs are Finite Element Analysis (FEA) and Computational Fluid Dynamics (CFD). These techniques have different use cases, but often work together to provide holistic visibility into a product’s performance. Overall, in this blog, we are going to highlight some of the ways in which FEA & CFD work together to shape engineering design and empower engineers to innovate with confidence.
What is FEA?
Finite Element Analysis or FEA is a computer-based statistical method to calculate when and how a product will react against actual forces like vibration, heat, stress, and other physical effects. FEA aids engineers in solving problems by breaking down a complex structure into smaller, manageable pieces or finite elements.
- Structural mechanics
- Thermal analysis
- Dynamic behavior
FEA is commonly used in various fields including aerospace, automotive, and civil engineering to corroborate the safety, functionality, and reliability of products.
What is CFD?
CFD stands for Computational Fluid Dynamics, which deals with the behavior of fluids (liquids and gases) and their interaction with surfaces. CFD, by solving the Navier-Stokes equations, allows engineers to study:
- Fluid flow
- Heat transfer
- Aerodynamics
- Chemical reactions
CFD is important for systems where fluid motion is a critical component (e.g. automotive, energy, HVAC, marine engineering, etc.) so the CFD must be integrated into the design optimization process.
The Synergy Between FEA and CFD
Although they are established as separate disciplines (mechanical behavior vs fluid dynamics), they are often used in conjunction as simulation solutions are integrated to aid in getting more accurate and comprehensive results for the engineering designs. So, how do these two methodologies complement each other
Thermal Analysis and Heat Transfer
- On the other hand, FEA is amazing for determining thermal stresses inside a solid body, and CFD does a great job predicting heat transfer around a body moving through the fluid.
- For example, in engine design, CFD can simulate airflow and heat dissipation in the cooling system, and FEA can analyze some thermal stresses on components.
Structural and Fluid Interactions (FSI)
- FSI or Fluid-Structure Interaction, is where FEA and CFD can converge. FSI simulations take into account how the fluid flow impacts a structure and how a structure impacts the flow.
- Applications include the design of aircraft wings that need to resist aerodynamic loads, or bridges that must hold under wind loads.
Design Optimization
- CFD is used by engineers to refine fluid flow properties like drag reduction or enhanced heat transfer.
- On the other hand, FEA ensures the structural integrity of the design during operating conditions.
- This trick allows the optimization of instanced shape and topology variables — for example, the shape of the arms and the topology of the structure behind the arms (airfoil versus wing) can be optimized at the same time, yielding both a better aerodynamics and mechanical stability for a wind turbine
Failure Prediction and Mitigation
- CFD can reveal where fluid forces could lead to wear or erosion, as in pipelines or turbine blades.
- FEA can then evaluate the structural implications of these forces, allowing for the prediction of component failure conditions, so that if necessary, an engineer can design around them.
Benefits of Integrating FEA and CFD in Engineering Design
Combining FEA and CFD allows engineers to realize multiple advantages:
Enhanced Accuracy : By addressing both structural and fluid-related challenges, FEA and CFD together give a more complete picture of a product’s behavior
Cost and Time Efficiency : Early simulations save time, costs and resources through virtual prototypes, speeding up the design process.
Improved Innovation : Architects can experiment with innovative design solutions that mediate structural integrity and fluid performance.
Risk Reduction : Thorough simulations leave little room for unwanted surprises to instigate an accident; and safety and reliability go hand in hand
Real-World Applications of FEA and CFD Integration
Aerospace Engineering
Similarly, in aerospace, Finite Element Analysis (FEA) guarantees aircraft components withstand extreme loads, and Computational Fluid Dynamics (CFD) optimizes aerodynamics for fuel efficiency and performance.
Automotive Design
CFD is used by automotive engineers to accomplish better airflow around vehicles and FEA is used to build structures that will withstand crash forces. Taken together, they make for safer, more efficient vehicles.
HVAC Systems
Conversely, in wind turbine design, CFD helps optimize the aerodynamics of the wind turbine blades, whereas FEA verifies that the wind turbine blades will remain intact under wind loads at very high speeds
Renewable Energy
In wind turbine design, CFD optimizes blade aerodynamics, and FEA ensures the blades can withstand high wind loads.
Challenges and Future Trends
Although the combination of FEA & CFD provides numerous benefits, it also brings difficulties, such as:
- High computational costs
- Model setup and data transfer are complex
- Lack of multidisciplinary expertise
But these challenges are being managed through increased software and hardware efficiency in the simulation arena. Their feasibility comes from emerging technologies like artificial intelligence and cloud computing, which are reducing the time and cost of performing FEA and CFD simulations. In conclusion, the future of engineering design will rely on harnessing these tools to develop more intelligent, sustainable solutions.
Conclusion:
FEA and CFD are both vital analyses in current engineering design, each dealing with different facets of a product’s performance. Together, these methods give engineers better insight into both structural and fluid dynamics, resulting in better-designed, more reliable products. Together, with the evolution of these simulation technologies, the strategic use of FEA and CFD will further enhance innovation and efficiency in engineering design.
Yes, FEA and CFD are related.FEA (Finite Element Analysis) is a numerical method used to solve problems in engineering and physics, including some aspects of
fluid dynamics. CFD (Computational Fluid Dynamics) is a field of study that uses numerical methods, including FEA, to solve problems related to fluid flow.
The Finite Element Method (FEM) is one of the numerical methods used in Computational Fluid Dynamics (CFD).
While the Finite Volume Method (FVM) is more commonly used in CFD due to its advantages in handling complex geometries and conservation properties,
FEM can be effectively applied to certain types of fluid flow problems, especially those involving complex material properties or intricate geometries.
FEM (Finite Element Method) is a general numerical method for solving partial differential equations. CFD (Computational Fluid Dynamics) is a field of study that uses numerical methods, including FEM, to solve problems in fluid flow.
Follow Milestone PLM Solutions for Mechanical Industry Updates, CAD Tips and Global Mechanical News.
Milestone PLM Solutions with its exclusive delivery center in India is a global CAD, CAM & FEA services outsourcing partner serving the needs of the Mechanical, Millwork and Automotive industry since 2004. MILESTONE focuses on the unique needs of clients and believes in tackling real-life problems with efficiency, smooth and ease.
The MILESTONE team can assist you with Product Design, 3d Modeling, Drafting & detailing, Reverse Engineering, FEA Analysis and more. We support multiple software including AutoCAD, SolidWorks, Catia, NX, Inventor, Solidedge & Ansys etc. Our approach is to provide a dedicated team for each customer over ongoing project and deliver the quality output consistently.
With our state of art technology and large talent pool of Engineers, we are developing best in class solutions for our customers across the globe. We align with your culture and values to form unbreakable partnerships and are primed for success with over 100 employees and 150 customers in the US, Europe, India, and Asia.
You can email us at info@milestonetech.net and can log in to our website www. milestonetech.net to know more about our services and our work portfolio or contact us on +1-844-598-0005