How AI and IoT are Shaping the Digital Manufacturing Landscape
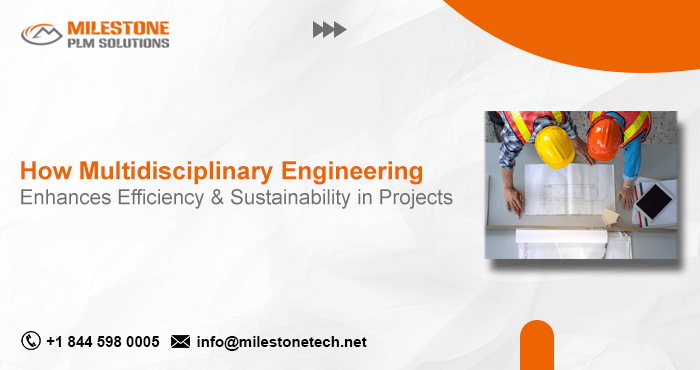
The manufacturing industry has always been at the forefront of technological advancements, embracing innovations to enhance efficiency, productivity, and scalability. In recent years, two transformative technologies, Artificial Intelligence (AI) and the Internet of Things (IoT), have taken center stage, reshaping the digital manufacturing landscape. Together, these technologies are revolutionizing how manufacturers design, produce, and manage their operations, enabling smarter, more efficient, and resilient factories.
This blog explores the convergence of AI and IoT in digital manufacturing, their key applications, and the benefits they bring to the industry.
Understanding Digital Manufacturing
Digital Manufacturing refers to the integration of advanced digital technologies into manufacturing processes to optimize production, streamline workflows, and enhance decision-making. It leverages data, analytics, and connectivity to create a more agile and efficient production environment. Digital manufacturing encompasses technologies like AI, IoT, robotics, cloud computing, and augmented reality, which work together to transform traditional manufacturing into a highly responsive and intelligent ecosystem.
The Role of IoT in Digital Manufacturing
The Internet of Things (IoT) is pivotal in digital manufacturing by connecting devices, machines, and systems through the internet, enabling real-time data exchange and communication. IoT transforms manufacturing facilities into smart factories where devices work cohesively to optimize operations.
Key Applications of IoT in Digital Manufacturing
- Smart Sensors and Predictive Maintenance: IoT-enabled sensors are embedded in machines to monitor their performance in real-time. These sensors collect data on temperature, vibration, and other parameters, which AI algorithms analyze to predict potential failures. This predictive maintenance reduces downtime, minimizes repair costs, and extends equipment lifespan.
- Connected Supply Chains: IoT devices enhance supply chain visibility by tracking inventory levels, shipments, and production processes. This real-time data helps manufacturers identify bottlenecks, streamline logistics, and ensure timely deliveries, creating a more efficient and reliable supply chain.
- Energy Management: Smart factories use IoT to monitor energy consumption across devices and systems. By analyzing this data, manufacturers can identify energy-saving opportunities, optimize processes, and reduce operational costs while achieving sustainability goals.
- Digital Twins: IoT enables the creation of digital twins—virtual replicas of physical assets. Manufacturers use digital twins to simulate and analyze production processes, optimize machine configurations, and test new designs before physical implementation, reducing errors and costs.
How AI Enhances Digital Manufacturing
While IoT provides the data, Artificial Intelligence (AI) analyzes it to extract valuable insights, automate decision-making, and improve efficiency. AI leverages machine learning, computer vision, and natural language processing to address complex manufacturing challenges.
Key Applications of AI in Digital Manufacturing
- Predictive Analytics and Demand Forecasting: AI algorithms analyze historical and real-time data to predict demand patterns. This helps manufacturers optimize production schedules, reduce excess inventory, and respond effectively to market fluctuations.
- Quality Control and Inspection: AI-powered computer vision systems inspect products for defects with high precision, significantly improving quality assurance processes. These systems identify minute flaws that are often missed by human inspectors, ensuring consistent product quality.
- Process Optimization: AI optimizes manufacturing processes by analyzing data from multiple sources, identifying inefficiencies, and suggesting improvements. For example, AI can recommend adjustments to machine settings to enhance output quality and reduce waste.
- Autonomous Robots and Cobots: AI drives autonomous robots and collaborative robots (cobots) that perform tasks such as material handling, assembly, and packaging. These robots adapt to changing production needs, work safely alongside humans, and increase overall efficiency.
The Synergy Between AI and IoT in Digital Manufacturing
The true potential of digital manufacturing lies in the convergence of AI and IoT. Together, these technologies create a powerful ecosystem where IoT devices collect vast amounts of data, and AI algorithms process and analyze this data to enable intelligent decision-making.
Real-World Examples of AI and IoT Synergy
- Predictive Maintenance at Scale: IoT sensors monitor machine health, and AI analyzes the data to predict when maintenance is needed. This prevents unexpected breakdowns, reduces downtime, and enhances operational efficiency.
- Smart Factory Automation: AI-powered systems control IoT-connected devices to automate manufacturing processes. For instance, AI can adjust production line speeds based on real-time demand data, ensuring optimal resource utilization.
- Dynamic Supply Chain Management: IoT provides real-time supply chain data, while AI uses this information to optimize logistics, predict demand, and recommend adjustments to production schedules. This ensures a more agile and responsive supply chain.
- Enhanced Worker Safety: AI and IoT combine to create safer working environments. IoT sensors detect hazardous conditions, while AI analyzes this data to implement safety protocols, such as shutting down equipment in dangerous scenarios.
Benefits of AI and IoT in Digital Manufacturing
- The integration of AI and IoT in digital manufacturing offers numerous benefits:
- Increased Efficiency: Automated processes and real-time insights reduce inefficiencies, streamline operations, and boost productivity.
- Cost Savings: Predictive maintenance, optimized energy consumption, and waste reduction lower operational costs.
- Improved Quality: AI-powered quality control ensures consistent product standards, reducing defects and rework.
- Agility and Scalability: Manufacturers can quickly adapt to changing market demands and scale their operations effectively.
- Sustainability: Smart energy management and waste reduction contribute to greener manufacturing practices.
Challenges and Future Outlook
Despite its transformative potential, adopting AI and IoT in digital manufacturing comes with challenges. These include high implementation costs, data security concerns, and the need for a skilled workforce. However, advancements in technology, coupled with decreasing costs, are making these solutions more accessible to manufacturers of all sizes.
Looking ahead, the future of digital manufacturing will be defined by greater integration of AI and IoT with emerging technologies like 5G, blockchain, and edge computing. These advancements will further enhance connectivity, data security, and real-time processing capabilities, paving the way for smarter and more resilient manufacturing ecosystems.
Conclusion:
AI and IoT are revolutionizing the digital manufacturing landscape by enabling intelligent, data-driven decision-making and automation. From predictive maintenance to quality control and supply chain optimization, their applications are transforming every aspect of manufacturing. As manufacturers continue to embrace these technologies, they can look forward to enhanced efficiency, cost savings, and sustainable growth.
By leveraging the synergy between AI and IoT, manufacturers can create smart factories that are not only efficient and resilient but also capable of thriving in a rapidly evolving industrial landscape. The future of digital manufacturing is here, and it is intelligent, connected, and full of possibilities.
AI enhances efficiency, reduces downtime, improves quality control, enables predictive maintenance, optimizes production processes, and facilitates supply chain management, leading to cost savings and improved productivity in manufacturing operations.
IoT enables real-time monitoring, predictive maintenance, improved asset utilization, enhanced supply chain management, and seamless communication between devices, resulting in smarter, more efficient, and connected manufacturing operations.
AI enhances digital manufacturing by optimizing design, automating processes, predicting equipment failures, enabling real-time decision-making, and improving efficiency, accuracy, and innovation across production and supply chain activities.
IoT collects data from connected devices, while AI analyzes and interprets it. Together, they enable smart decision-making, predictive analytics, automation, and optimization in various industries, especially in manufacturing.
Follow Milestone PLM Solutions for Mechanical Industry Updates, CAD Tips and Global Mechanical News.
Milestone PLM Solutions with its exclusive delivery center in India is a global CAD, CAM & FEA services outsourcing partner serving the needs of the Mechanical, Millwork and Automotive industry since 2004. MILESTONE focuses on the unique needs of clients and believes in tackling real-life problems with efficiency, smooth and ease.
The MILESTONE team can assist you with Product Design, 3d Modeling, Drafting & detailing, Reverse Engineering, FEA Analysis and more. We support multiple software including AutoCAD, SolidWorks, Catia, NX, Inventor, Solidedge & Ansys etc. Our approach is to provide a dedicated team for each customer over ongoing project and deliver the quality output consistently.
With our state of art technology and large talent pool of Engineers, we are developing best in class solutions for our customers across the globe. We align with your culture and values to form unbreakable partnerships and are primed for success with over 100 employees and 150 customers in the US, Europe, India, and Asia.
You can email us at info@milestonetech.net and can log in to our website www. milestonetech.net to know more about our services and our work portfolio or contact us on +1-844-598-0005