Why Geometric Dimensioning & Tolerancing Matters in Modern Manufacturing
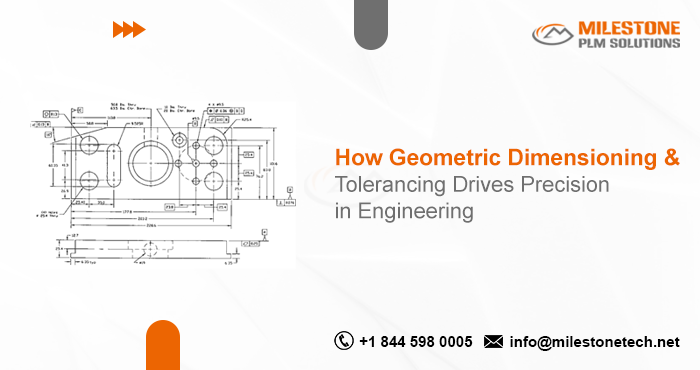
In the quick pacing and changing environment of contemporary manufacturing, accuracy has become a basic need rather than simply something to be enjoyed. Yes, Geometric Dimensioning & Tolerancing (GD&T) is one of the main tools to make sure that all parts and assemblies are built accurately to specifications Keywords: Whether Naturally Draftable, GD&T(drbl), IT Process Automation Tools So what is GD&T exactly, and why is it so important in the modern manufacturing world? In this blog, we will be discussing the importance of GD&T ALL, when do you require it and how does it help to manufacture quality while keeping costs in check.
Understanding Geometric Dimensioning & Tolerancing (GD&T)
GD&T stands for Geometric Dimensioning & Tolerancing, and it is a system which allows you to define engineering tolerances using symbols and notations on drawings. GD&T differs from traditional dimensioning in that it does not merely spew out lines of linear dimensions (length, width, height) one after the other; rather it provides a specific description of the geometry of a part. It includes how features relate in terms of their functional relationships with other features of the part such as the form, orientation, location and size.
The system uses a set of symbols and rules to convey important information, such as:
- Form: Shape of individual features (e.g., flatness, straightness, circularity)
- Orientation: Angles between features (e.g., parallelism, perpendicularity, angularity)
- Location: Position of features relative to others (e.g., position, concentricity, symmetry)
- Runout: The deviation of a feature from a perfect form during rotation
GD&T is critical because it provides a clear and concise method for communicating these complex relationships and tolerances. This is vital in an industry where parts often have to fit together seamlessly in complex assemblies.
Why GD&T Matters in Modern Manufacturing
Enhanced Precision and Consistency
Modern manufacturing processes rely heavily on automation, CNC machines, and robotic systems. For these technologies to function correctly, they require high levels of precision and consistency. GD&T offers a universal language for designers, engineers, and manufacturers, ensuring that each part produced meets the required specifications without ambiguity.
Using GD&T ensures that parts are made with consistent tolerances, allowing them to fit correctly in assemblies. Even with mass production, GD&T ensures that the final product meets the exact specifications needed for functionality, durability, and safety. Without this precision, manufacturers would face challenges with parts that are either too loose or too tight, which can lead to costly delays and waste.
Reduced Errors and Improved Quality Control
The importance of GD & T is quite crucial to locale the errors at manufacturing end. It minimizes ambiguity between design and production teams by clearly specifying the range of permissible variation for each feature. Furthermore, GD&T offers detailed requirements for quality control inspectors, ensuring that each component is compared to the correct standard.
Defining the part using GD&T makes it simpler and clearer for quality control personnel to measure the component to verify that it conforms to the drawing. Thus lower the chances of defects and enhanced quality of end product. GD&T is crucial in industries where tolerancing at the millimetre precision matters, such as aerospace, automotive and medical device manufacturing.
Cost Savings
GD&T is great because of one main reason: it saves you money! GD&T reduces scrap and rework by ensuring that parts are manufactured correctly the first time. This creates expensive downtime and the scrap of entire batches of parts when parts go out-of-tolerance. On the other hand, GD&T is often considered as a means for manufacturers to achieve more efficient production processes and waste.
Moreover, GD&T enables improved communication between design and manufacturing teams. They help ensure everyone has the same expectations so costly errors and rework down the line during production is less likely. It also means lower costs and faster turnaround times, as well as freeing up resources.
Improved Collaboration Between Teams
As manufacturing styles have evolved, we need different teams to work together—design, engineering, production, and quality control. GD&T is a common language which connects these teams. It allows the designers to express how they are thinking, and engineers can interpret how that thought translates into a process that can be manufactured.
For instance, a design engineer could employ GD&T symbols to delineate important characteristics of a component, like where precisely holes should go or whether two faces are parallel. This can then allow production teams to configure the machines correctly, therefore producing the part properly. By using GD&T, the transfer of information across teams becomes a lot more comfortable and this helps to reduce errors or miscommunication.
Enhanced Product Performance and Functionality
For most industries, the functional performance of a product relies heavily on the perfectly aligned pieces of these components. Take the automotive industry – a slight variation in position or orientation of an important feature can impact the functioning of a vehicle. GD&T guarantee that the parts and assemblies are manufactured to desired levels of accuracy, enhancing product functionality and performance.
Equipment such as a shaft and bearing should be aligned properly so that the in between space wear out much faster and either be a catastrophic failure of entire assembly. It also ensures that parts are located and oriented within acceptable limits, facilitating part interchangeability while increasing working dependability and durability of the product.
Facilitating Advanced Manufacturing Techniques
With manufacturing evolving with 3D printing and additive manufacturing, among other roles for GD&T become even more crucial. These new processes usually call for an alternate means of tolerancing and part inspection. Since these technologies can create highly complex features, GD&T offers a compatible framework that maximizes the potential of these technologies for manufacturers.
For instance, with 3D printing, parts are built upon one another layer by layer which causes geometric discrepancies. GD&T can define the limits of some variations on part geometry that will not affect adherence to specifications and functionality of the resulting printed part.
Conclusion:
With the modern manufacturing environment where precision, efficiency and collaboration on global scale are at its peak, exact approaches to dimensional measurement and specification must be exercised in order to eliminate ambiguity during a product design cycle.GD & T engineering services must play an important role here. GD&T gives your workforce a uniform language with which to communicate part specifications, making it possible to manufacture parts right the first time, every time and in turn eliminating errors, as well as enhancing quality and bottom-line savings. GD&T will always be a core method through which products can continue to satisfy the expectations of users as production technologies progress.
GD&T (Geometric Dimensioning and Tolerancing) ensures precise communication of part tolerances, improving consistency and quality in manufacturing. It reduces errors, minimizes waste, and facilitates better fit and function of parts, enhancing overall productivity and efficiency.
Using geometrical tolerance in production ensures precise control over part dimensions, enhancing consistency and interchangeability. It reduces material waste, improves quality, and simplifies inspections, ultimately lowering costs while ensuring parts meet functional requirements and fit accurately in assemblies.
Properly implemented GD&T reduces manufacturing costs by minimizing errors, reducing rework, and improving communication. It ensures precise tolerances, leading to faster assembly and higher-quality parts, ultimately reducing waste, material costs, and production time.
GD&T (Geometric Dimensioning and Tolerancing) improves design accuracy, reduces manufacturing errors, enhances communication between teams, and ensures consistent product quality. It provides clear tolerance guidelines, minimizing rework and costs, leading to efficient production and higher-quality outcomes.
Geometric Dimensioning and Tolerancing (GD&T) is crucial for precision manufacturing. It standardizes communication, ensures accurate part specifications, reduces errors, and enhances interoperability between design and production teams, ultimately improving quality, efficiency, and cost-effectiveness in engineering and manufacturing processes
Geometric Dimensioning and Tolerancing (GD&T) is a system that defines engineering tolerances precisely. It improves part quality by specifying allowable variations in geometry, ensuring parts fit and function as intended, reducing errors, and streamlining production.
Follow Milestone PLM Solutions for Mechanical Industry Updates, CAD Tips and Global Mechanical News.
Milestone PLM Solutions with its exclusive delivery center in India is a global CAD, CAM & FEA services outsourcing partner serving the needs of the Mechanical, Millwork and Automotive industry since 2004. MILESTONE focuses on the unique needs of clients and believes in tackling real-life problems with efficiency, smooth and ease.
The MILESTONE team can assist you with Product Design, 3d Modeling, Drafting & detailing, Reverse Engineering, FEA Analysis and more. We support multiple software including AutoCAD, SolidWorks, Catia, NX, Inventor, Solidedge & Ansys etc. Our approach is to provide a dedicated team for each customer over ongoing project and deliver the quality output consistently.
With our state of art technology and large talent pool of Engineers, we are developing best in class solutions for our customers across the globe. We align with your culture and values to form unbreakable partnerships and are primed for success with over 100 employees and 150 customers in the US, Europe, India, and Asia.
You can email us at info@milestonetech.net and can log in to our website www. milestonetech.net to know more about our services and our work portfolio or contact us on +1-844-598-0005