Development and Designing of Transportation Vehicle
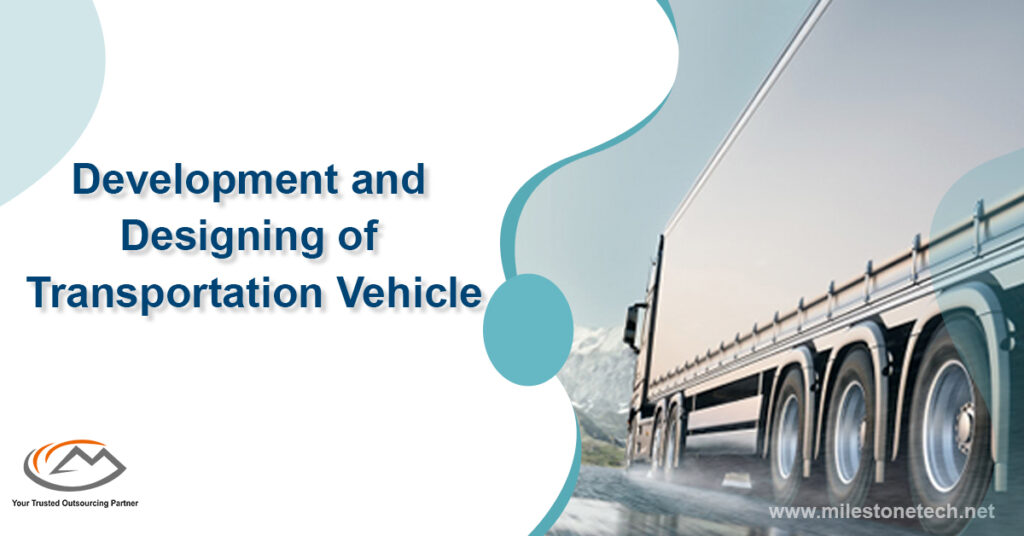
Transportation is an important part of economic development. Rural and urban populations both need these vehicles to keep industries running, transport, and even defend the country. With new innovations in transportation technology, vehicles are able to keep up with the challenges of modern life.
A vehicle development process typically takes an idea to a product and back. This includes anything from our initial thought, screening it against other ideas, creating a concept, functional testing, marketing strategy and finally commercializing the finished product. When a company is developing a new vehicle, they need to decide if they are going to keep it the same or change it. Consumer adoption plays an important role in this decision. It helps in spreading awareness of new product development and increase the interest among consumers for evaluation and trial before acceptance.
The Development and Designing of any transportation vehicle require the use of construction, configuration, and styling. Designs should account for technical innovation and refinement during production. Earlier manufacturers used a wooden framework for upper body work, but metal chassis frames were needed for high cars. The 19th century saw the development of vehicles powered by steam engines. The advancement allowed for new advancements in cooling, valve and carburation systems. This resulted in an utter rivalry between steam engines, diesel and petrol, over the course of that century. Though all three types of engines possess common mechanical characteristics, with diesel engines being run by combustion rather than ignition by electric sparks. This eliminates the need for a carburetor and a spark ignition system, making them increasingly popular within challenging conditions.
The materials needed for the construction of vehicles include iron, copper, and aluminum. These materials provide various properties such as ductility, strength, and stiffness under various conditions. When a vehicle is functioning in an environment with high humidity or salt content, their corrosion stability must be maxed out to ensure longevity in such environments. Polymers and ceramics have helped transportation companies to create supreme vehicles and improve the durability of their other parts. These materials are also light and they are instrumental in making transportation vehicles that function better.
Transportation vehicle design has made an enormous leap in the late 20th century by employing just-in-time/lean production philosophy in the manufacturing . It has increased flexibility and agility, leading to better production of customizable products. The approach identifies problems at any stage of development and allows institutions to go with less bottlenecks, errors, delays and high inventories. Industrial designers can maximize manufacturing opportunities by analyzing requirements and target outcomes. This technique allows designers to use various techniques for the design process, such as IPPD, in order to scrutinize the requirements of a product and fine tune it according to its specific needs.
It’s important to analyze vehicle designs as early as possible. Designers first do drawings and then turn them into 3D models. The process provide all the design information for tools and structures. Prototypes can take a long time, but they help provide the maximum performance data. Computer aided design software is being used to make vital decisions in the designing process.
The aerodynamics of vehicles affects the shape and design. This has driven the opportunity for greater technology to be introduced into designing more fuel efficient vehicles. The efficiency of a vehicle relies on its engine’s efficiency, its weight, and aerodynamic drag. Some important factors in the performance of any vehicle are aerodynamics, drag reduction techniques, stability during crosswinds, noise levels and cabin ventilation. A lot of these factors are stabilized through computational fluid dynamics.
There are five major loads for a transportation vehicle: bending, torsion, combined bending and torsion, lateral load, and front and back load. When traversing on roads and other surfaces vehicle loads are imposed on the vehicle. The bending and torsion loads can be examined by using surface stress that is generally used to measure local stresses and deflections. This facilitates the design of the vehicle’s structure. Finite element methods are used on the traditional engineering design to achieve greater detail and better efficiency in the structure.
The importance of a vehicle’s crash-worthiness is realized by looking at how well it performs under various collision scenarios. Manufacturers study how the car performs in crashes with a rigid barrier and between two vehicles for safety purposes. Crash dummies are used to emulate human responses to the impacts and analyze any potential car seat belt failures. There are four common areas of concerns that manufacturers seek to improve: intrusion caused by the collapse of the passenger compartment, seat belt extension which can cause passengers to strike something in the vehicle like the steering wheel, transmission of localized loads from high deceleration forces, and seat belt webbing failure.
Manufacturers focus on vibrations and noise pollution, to ensure a comfortable driving experience. Today with the reduction in vehicle weight and higher engine speeds, designers pay more attention to reducing vibration and noise by various approaches like mathematical modeling.
Feedback allows businesses to improve the products and services that they offer. By responding to customer feedback, businesses can be sure that the customers are satisfied with their service. Monitoring post-market surveillance helps companies see any flaws in the design or manufacturing of the product so that improvements can be made.
Follow Milestone PLM Solutions for Mechanical Industry Updates, CAD Tips and Global CAD, CAM & FEA News.
Milestone PLM Solutions with its exclusive delivery center in India is a global CAD, CAM & FEA services outsourcing partner serving the needs of the Mechanical, Millwork and Automotive industry since 2004. MILESTONE focuses on the unique needs of clients and believe in tackling real-life problems with efficiency, smooth and ease.
The MILESTONE team can assist you with Product Design, 3d Modeling, Drafting & detailing, Reverse Engineering, FEA Analysis and more. We support multiple software including AutoCAD, Solidworks, Catia, NX, Inventor, Solidedge & Ansys etc. Our approach is to provide a dedicated team for each customer over ongoing project and deliver the quality output consistently.
With our state of art technology and large talent pool of Engineers, we are developing best in class solutions for our customers across the globe. We align with your culture and values to form unbreakable partnerships and are primed for success with over 100 employees and 150 customers in the US, Europe, India, and Asia.
For more queries regarding any of the above-mentioned topics, feel free to connect with us on our website www.milestonetech.net or contact us on +1-844-598-0005