Boosting Innovation with Computer-Aided Engineering (CAE) Tools
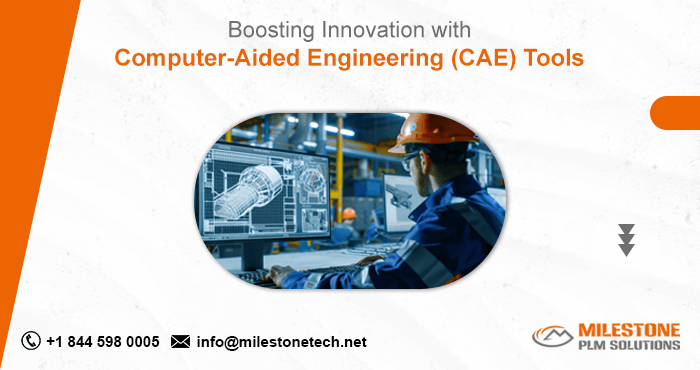
As we operate in an increasingly fast-paced industrial landscape the need to be efficient, innovative and deliver quality products has never been greater. Computer-Aided Engineering (CAE) tools have become key technologies that facilitate intellectual inquisitiveness and speed innovation, as well as reduce development costs and time for engineers & designers. With companies from automotive to aerospace, electronics and more realizing the value of digital tools, CAE is no longer a nice-to-have – it’s crucial for remaining competitive. In this blog, we are going to see how CAE tools are giving us innovation, productivity to our traditional engineering process.
What is Computer-Aided Engineering?
Computer-Aided Engineering (CAE) Simulation software is used to simulate the performance of a product, optimize design for better functionality and analyze manufacturing process. Some examples of CAE tools are simulations FEA, MBD and CFD which help engineers to analyze the various dynamics aspects (structure deformation) at an early stage itself.
Accelerated Product Development
These tools for accelerated product development make it much faster to settle design details (since engineers test their products through simulations long before any physical prototypes are built) … Simulation-driven design enables development teams to significantly reduce the number of costly physical prototypes they build and close prototype test iterations faster, helping companies bring game-changing new products in half the time. This simply reduces the cost to rework in later stages, an thing that is directly proportional with analyzing CAE.
Enhanced Design Quality and Precision
These tools for accelerated product development make it much faster to settle design details (since engineers test their products through simulations long before any physical prototypes are built) … Simulation-driven design enables development teams to significantly reduce the number of costly physical prototypes they build and close prototype test iterations faster, helping companies bring game-changing new products in half the time. This simply reduces the cost to rework in later stages, an thing that is directly proportional with analyzing CAE.
Cost-Effective Prototyping and Testing
Physical prototyping and testing performed in traditional product development are costly and takes more time. Even engineers can perform virtual tests and analyzes at least with the CAE tools, thus reducing the reliance on physical prototypes. For this reason, CAE allows engineers to optimize a product and test scenarios digitally which saves thousands of dollars on material and labor. Not only is this a cost-saving, no-waste solution as our world becomes increasingly more about the sustainable engineering practices of today.
Improved Collaboration Across Disciplines
Today’s CAE tools allow workflows that can be linked with other design and simulation software, promoting the sharing of information between various engineering disciplines. For example, engineers performing structural analysis can collaborate with other engineers working on thermal analyses and fluid dynamics in the same toolset — streamlining workflows across all disciplines. This is a step towards genuinely integrated vehicles and cross-functional teams that work together in tandem to further product outcomes, drive innovation.
Optimization for Complex Systems
When products are more complex, the imperative for strong and optimized designs is essential. Optimization: Since CAE tools allow the user to assess many design variations, it is easy for them to find out which one provides a maximum solution subjected with certain constraints. Through sophisticated optimization algorithms, engineers can factor in considerations of weight, material usage and energy efficiency for overall product performance that have achieved a new generation of stringent standards.
Key CAE Tools for Innovation
- Finite Element Analysis (FEA): Every product has to withstand stresses, strains and thermal effects under operating conditions; evaluating optimum structural performance & durability is facilitated by FEA.
- Computational Fluid Dynamics (CFD): It is typically used for situations in which the fluid flow of heat transfer and its related phenomena are important, such as aerospace and automotive industries.
- Multibody Dynamics (MBD): MBD tools let engineers analyze the movement and interaction between multiple connected elements, ideal for mechanical systems such as automotive suspension or machinery.
Real-World Applications of CAE in Engineering
A large selection of applications make CAE tools vital in industrial settings. In automotive engineering, CAE cyber simulations play with scenarios of vehicle safety,fuel efficiency and aerodynamics testing resulting in lighter, more efficient as well as safer vehicles. When servicing the aerospace field, CAE is used to analyze how aircrafts will perform under different flight conditions which help in reducing weight and improving safety. Thermal management in electronics: CAE tools are also used to ensure reliable products under harsh operating environments with respect structural integrity of components as well.
The Future of CAE and Engineering Innovation
As technologies like Artificial Intelligence (AI) and Machine Learning (ML) integrate into CAE, the capabilities of these tools are set to expand significantly. AI-driven optimization, predictive analytics, and automated design generation will make CAE tools even more powerful. Engineers will be able to analyze massive datasets to identify patterns and optimize designs faster than ever before, transforming the way products are conceived and developed.
Conclusion:
The boundaries of innovation in engineering are being reimagined with Computer-Aided Engineering (CAE) tools. CAE has introduced groundbreaking development cycles, cost-effective prototyping, higher levels of precision and interdisciplinary collaboration in all companies which is now what really enable those to push forward with innovation at scale. These tools will only grow in the years to come and remain instrumental for shaping the future of product design & engineering by enabling challenging possibilities that drive an industry forward. This isn’t about being better than your competitors — this is leading an entire market forward towards a more innovative and efficient way of designing.
Follow Milestone PLM Solutions for Mechanical Industry Updates, CAD Tips and Global Mechanical News.
Milestone PLM Solutions with its exclusive delivery center in India is a global CAD, CAM & FEA services outsourcing partner serving the needs of the Mechanical, Millwork and Automotive industry since 2004. MILESTONE focuses on the unique needs of clients and believes in tackling real-life problems with efficiency, smooth and ease.
The MILESTONE team can assist you with Product Design, 3d Modeling, Drafting & detailing, Reverse Engineering, FEA Analysis and more. We support multiple software including AutoCAD, SolidWorks, Catia, NX, Inventor, Solidedge & Ansys etc. Our approach is to provide a dedicated team for each customer over ongoing project and deliver the quality output consistently.
With our state of art technology and large talent pool of Engineers, we are developing best in class solutions for our customers across the globe. We align with your culture and values to form unbreakable partnerships and are primed for success with over 100 employees and 150 customers in the US, Europe, India, and Asia.
You can email us at info@milestonetech.net and can log in to our website www. milestonetech.net to know more about our services and our work portfolio or contact us on +1-844-598-0005