Computational Fluid Dynamics Role in Product Manufacturing
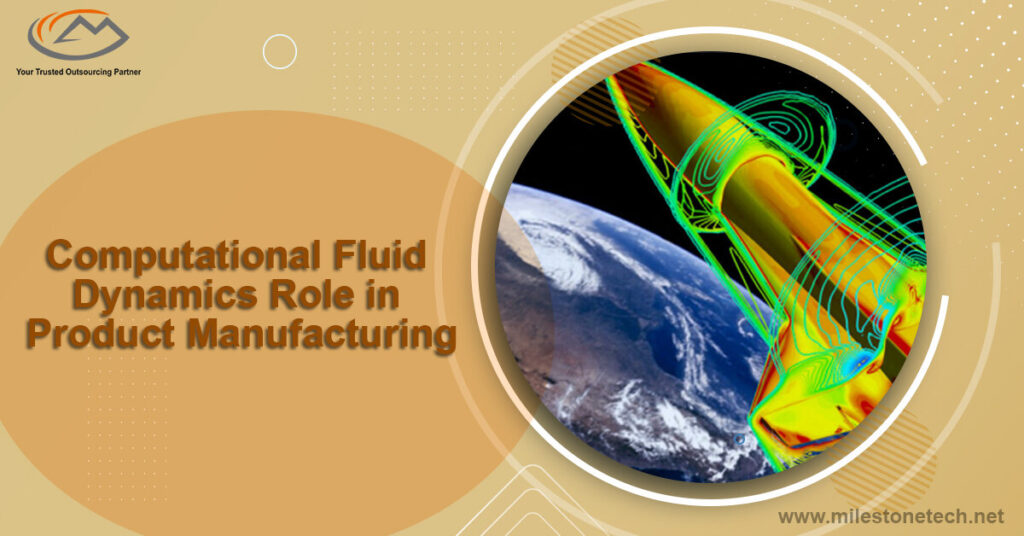
CFD – Computational Fluid Dynamics or CFD involves the analysis of fluid flow, heat transfer, and associated systems with the help of computer-based simulation. It has a wide range of industrial applications and is a very robust tool for product manufacturing. It is excessively used in automobile industries for, among other things, predicting drag forces and lift of the vehicle. CFD is a very specific type of software, depending on knowledge in fluid dynamics, mathematics, and programming. It involves assuming the wide-ranging of variables to generate systems.
Computational Fluid Dynamics is used to analyze the lift and drag of vehicles. With hydrodynamics of ships, this technique can be utilized to analyze their performance.The technique can be used in studies of combustion engines, power plants, and rotating passages. It is also useful for blood flow analysis in veins and arteries.The technique can be used to determine the distribution of effluents and pollutants.
Industrial units find computational fluid dynamics to be quite awe-inspiring. Computational Fluid Dynamics lets you have access to unlimited minutes of details that help with designing complex systems, which reduces the time and cost of system design. Computational fluid dynamics can also analyze a system to determine whether drastic conditions like disasters can be mitigated without compromising its Computational Fluid Dynamics provides a huge volume of results, without added cost and it is very cheap to perform. Experimental studies in the industry are being ignored due to variability in factors like hiring personal, performance level and other aspects.
Fluid flow problems can be addressed by utilizing code which cover the numerical algorithms and provides a smooth access to solve difficult fluid flow problems. These codes consist of a pre-processor, a solver, and a post-processor.
CFD is useful in designing a material’s shape and flow. “CFD is the simulation of fluid flows at a variety of scales, from 30 micrometers to several kilometers.” The input of this fluid problem creates a “domain” that is usually defined by the geometry. For example, the boundary of an object made out of a specific material. CFD can transform this “domain”, or boundary, into an easier to manufacture object with less material waste.CFD is usually used to model fluid properties like temperature, pressure, etc. It can be used in any environment where two physical objects interact. A CFD solution’s accuracy depends on how many cells are in the grid. The more cells there are, the higher chance of a accurate solution for your simulation since more detail was modeled.
Three numerical calculation methods are used to find solutions for fluid flow: finite difference, finite element, and spectral. The most common of these is finite difference. In order to calculate an approximation of physical process, a matrix equation is set up using the basic equations that govern fluid flow. It is then solved by iterative methods, which can be algebraic or numerical. The main difference between finite volume and other CFD techniques is that control volumes are used in the former.Computational fluid dynamics codes consist of discretion techniques that are helpful for convection and diffusion’s, among other aspects of fluid flow. The conservation of various flow variables such as enthalpy and velocity will consistently be expressed to estimate whether it increases or decreases. The simple concept that the equations have the same properties for each finite-size cell will make it easy for engineers to understand an ordinary transparent fluid flow as compared to other methods.
As the popularity of CFD software increases, the processing capabilities have become more sophisticated. It now provides graphical capabilities along with domain geometry and grid display. The software package also includes vector plots and line or shaded contour plots, which are further enhanced by animated and dynamic result displays. This has allowed transmission of ideas to people who don’t have engineering backgrounds.
Fluid flow problems are a complex set of physics, chemistry, and mathematics. The user must have significant knowledge in the various subjects prior to simulating these problems. This requires skillful professionals who can identify and formulate the chemical and physical aspects of the flow problem. Key decisions that must be made while modeling fluid flow equations to preserve necessary characteristics of the problem are effects of ambient temperature, variations in air density, turbulent flow, and air bubbles, etc.The more detailed an equation is simplified for CFD simulations, the more accurate the simulation will be. Simulations may not be as accurate if there is a lot of deviation in geometry and grid design. A converged solution may be reached by using acceleration and relaxation to regulate convergence.
For these converged solutions, optimization is an issue. Providers with extensive experience in code evaluation should optimize these solutions. However, some require refinement because they are filled with errors. One needs to do grid dependence study to eliminate all error patterns of each algorithm and one needs a thorough knowledge of the algorithm to guess it if he can’t eliminate the error pattern.
Computational Fluid Dynamics (CFD) is a method of reorganizing fluid flows. It helps scientists study fluids with mathematical modeling, discretion, and other pre- and post-processing tools. CFD has helped the scientists develop more powerful computational tools to study fluid dynamics. CFD gives results equivalent to laboratory experiments.
The goal of growth in the CFD field is to offer a capability comparable with other CAE applications. The complexity of the existing behavior can’t be translated into an economical and complete representation, but CFD is still developing.
Computational fluid dynamics, a branch of physics, has seen resurgence in recent times. The upsurge in interest is largely due to the availability of affordable high-performance computing hardware and easy to use interfaces. CFD codes are extremely scalable and can generate large volume of solutions at no extra costs.
The accuracy and cost of a Computational Fluid Dynamics solution is dependent upon the size of the grid. With a larger grid, the accuracy and cost also increase. The ideal mesh will change in different areas around the body depending on what needs to be fixed most.
Follow Milestone PLM Solutions for Mechanical Industry Updates, CAD Tips and Global CAD, CAM & FEA News.
Milestone PLM Solutions with its exclusive delivery center in India is a global CAD, CAM & FEA services outsourcing partner serving the needs of the Mechanical, Millwork and Automotive industry since 2004. MILESTONE focuses on the unique needs of clients and believe in tackling real-life problems with efficiency, smooth and ease.
The MILESTONE team can assist you with Product Design, 3d Modeling, Drafting & detailing, Reverse Engineering, FEA Analysis and more. We support multiple software including AutoCAD, Solidworks, Catia, NX, Inventor, Solidedge & Ansys etc. Our approach is to provide a dedicated team for each customer over ongoing project and deliver the quality output consistently.
With our state of art technology and large talent pool of Engineers, we are developing best in class solutions for our customers across the globe. We align with your culture and values to form unbreakable partnerships and are primed for success with over 100 employees and 150 customers in the US, Europe, India, and Asia.
For more queries regarding any of the above-mentioned topics, feel free to connect with us on our website www.milestonetech.net or contact us on +1-844-598-0005