Common Mistakes in Assembly Drawing and How to Avoid Them
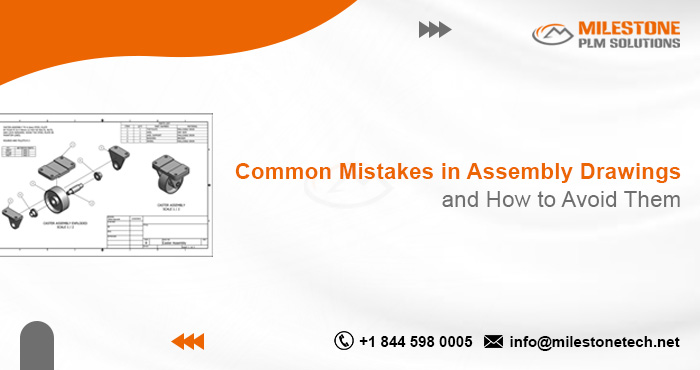
Assembly Drawing: Assembly drawing play a crucial role in manufacturing and engineering, providing a detailed blueprint for assembling components accurately. These drawings guide engineers, manufacturers, and technicians in ensuring seamless product development. However, errors in assembly drawing can lead to costly delays, manufacturing defects, and miscommunication.
In this blog, we will explore some common mistakes in assembly drawings and how to avoid them to enhance accuracy and efficiency.
Lack of Proper Dimensioning - Assembly Drawing
Mistake:
One of the most frequent mistakes in assembly drawing is incomplete or incorrect dimensioning. Missing or unclear dimensions can lead to misinterpretation, resulting in improper assembly.
Mistake:
- Ensure all critical dimensions are clearly defined.
- Use standard dimensioning techniques and follow industry guidelines.
- Double-check measurements before finalizing the drawing.
Inconsistent or Missing Annotations
Mistake:
Annotations such as part numbers, material specifications, and fastening instructions are often missing or inconsistent, leading to confusion during assembly.
Solution:
- Use clear, standardized annotations throughout the drawing.
- Cross-check part numbers and references with the Bill of Materials (BOM).
- Provide detailed assembly notes to avoid misinterpretation.
Poorly Defined Tolerances
Mistake:
Ignoring or incorrectly specifying tolerances can result in parts that do not fit properly, leading to manufacturing defects.
Solution:
- Define tolerances clearly based on industry standards.
- Use GD&T (Geometric Dimensioning and Tolerancing) principles to ensure precision.
- Ensure tolerances are achievable with the available manufacturing processes.
Overcrowded or Cluttered Drawings
Mistake:
Excessive detailing, overlapping annotations, or unclear linework can make assembly drawings difficult to interpret.
Solution:
- Maintain clarity by organizing elements logically.
- Use different line weights and colors (if applicable) to differentiate between sections.
- Keep the drawing neat and avoid excessive detailing where unnecessary.
Overcrowded or Cluttered Drawings
Mistake:
A missing or inaccurate BOM can cause assembly line issues, leading to incorrect part procurement or assembly errors.
Solution:
- Verify BOM details before finalizing the assembly drawing.
- Ensure part descriptions, quantities, and specifications match the actual requirements.
- Include a reference link between the drawing and the BOM for easy cross-checking.
Lack of Exploded Views -: Assembly Drawing
Mistake:
Without exploded views, complex assemblies may become difficult to understand, causing delays in production and errors in assembly.
Solution:
- Include exploded views for complex assemblies to provide a clear step-by-step visual representation.
- Label each component properly in the exploded view.
- Use appropriate line styles to show how parts fit together.
Ignoring Standardized Drawing Conventions
Mistake:
Failure to follow standard drawing conventions can make it difficult for other engineers or manufacturers to interpret the design correctly.
Solution:
- Adhere to industry standards such as ISO, ASME, or ANSI.
- Use proper symbols, line types, and drawing scales.
- Ensure consistency across all drawings within a project.
Omitting Assembly Instructions
Mistake:
Assembly instructions are often overlooked, making it challenging for technicians to assemble components correctly.
Solution:
- Provide clear step-by-step assembly instructions within the drawing.
- Include references to tools, tightening sequences, and safety precautions.
- Utilize callouts to highlight critical steps in the process.
Not Considering Manufacturing Constraints
Mistake:
Designers sometimes overlook manufacturing limitations, leading to designs that are difficult or costly to produce.
Solution:
- Consult with the manufacturing team during the design phase.
- Ensure materials, processes, and tolerances align with available capabilities.
- Optimize designs for manufacturability and ease of assembly.
Failing to Review and Validate Drawings
Mistake:
Skipping the review and validation process can lead to undetected errors that cause production delays and costly rework.
Solution:
- Conduct thorough design reviews with multiple stakeholders.
- Perform a final check using CAD software tools to detect errors.
- Validate the assembly drawing through prototyping or digital simulations before final release.
Conclusion- : Assembly Drawing
Assembly Drawing : – Avoiding these common mistakes in assembly drawing can significantly enhance manufacturing efficiency, reduce costs, and improve product quality. By ensuring proper dimensioning, clear annotations, accurate BOMs, and adherence to industry standards, engineers can create precise and error-free assembly drawings. Regular review and collaboration with manufacturing teams further improve the accuracy and usability of these drawings.
Follow Milestone PLM Solutions for Mechanical Industry Updates, CAD Tips and Global Mechanical News.
Milestone PLM Solutions with its exclusive delivery center in India is a global CAD, CAM & FEA services outsourcing partner serving the needs of the Mechanical, Millwork and Automotive industry since 2004. MILESTONE focuses on the unique needs of clients and believes in tackling real-life problems with efficiency, smooth and ease.
The MILESTONE team can assist you with Product Design, 3d Modeling, Drafting & detailing, Reverse Engineering, FEA Analysis and more. We support multiple software including AutoCAD, SolidWorks, Catia, NX, Inventor, Solidedge & Ansys etc. Our approach is to provide a dedicated team for each customer over ongoing project and deliver the quality output consistently.
With our state of art technology and large talent pool of Engineers, we are developing best in class solutions for our customers across the globe. We align with your culture and values to form unbreakable partnerships and are primed for success with over 100 employees and 150 customers in the US, Europe, India, and Asia.
You can email us at info@milestonetech.net and can log in to our website www. milestonetech.net to know more about our services and our work portfolio or contact us on +1-844-598-0005