Digital Twin Technology: Revolutionizing the Engineering Landscape
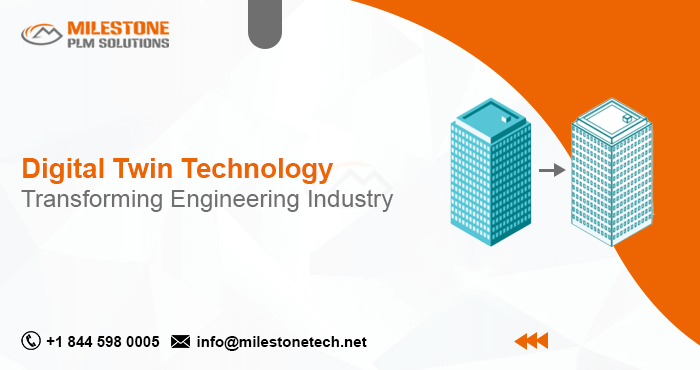
Digital Twin Technology: A Groundbreaking Technology for Engineering in Digital Age A Digital Twin is a digital counterpart of a physical object, system, or process that updates and evolves as its physical counterpart changes. By integrating Internet of Things (IoT), Artificial Intelligence (AI), and data analytics, Digital Twins also allow the engineers to monitor, analyze, and optimize the asset in a faster and more efficient manner.
How Digital Twins Are Transforming Engineering Practices
Enhancing Product Development and Simulation
Until now, product development for engineers was mainly a human activity where they created prototypes, tested, and inspected them before manufacturing. This reduces physical testing that consumes lots of time-to-market and money. Engineers can examine performance, detect possible defects, and make appropriate changes to ensure high quality products.
Driving Predictive Maintenance and Operational Efficiency
Accurately predicting maintenance needs is one of the most important benefits of Digital Twins. Digital Twins can predict long-term equipment performance, enabling engineers to make maintenance before potential failures occur. This allows for predictive maintenance, which minimizes downtime, enhances asset longevity, and maximizes efficiency.
Streamlining Supply Chain and Logistics
The Digital Twin Technology greatly helps in supply chain management with real-time tracking of logistics, inventory, and production processes. Use of Digital Twins and Simulation: Supply chain Digital Twins simulate multiple scenarios, allowing businesses to detect inefficiencies, anticipate disruptions, and optimize operational efficiency
Revolutionizing Infrastructure Planning and Sustainability
Digital Twins, serve up insights on the structural integrity, energy consumption and environmental impact of large-scale infrastructure projects — bridges, roads, smart cities. Engineers can model different scenarios, analyze risks, and make evidence-based decisions, all of which lead to a safer, greener and more cost-efficient work environment and product.
Exploring the Different Categories of Digital Twin Technology
Virtual Models for Products
Digital Twins Product Twins are used to create digital duplicates of single unit components or products. They enable manufacturers to simulate and test designs in virtual environments before proceeding to physical production, which lowers prototyping costs and increases product reliability.
Holistic Representation of Integrated Systems
System Twins provide a holistic view of interdependent things like manufacturing processes, industrial automation, and the entire production line. They assist engineers in optimizing workflows, identifying inefficiencies and improving collaboration between departments.
Infrastructure-Focused Digital Twins
Infrastructure Twins have applications across large-scale projects like smart cities, transport networks, and energy grids. They help plan for, monitor, and preserve urban infrastructure, facilitating long-term sustainability and resilience.
Unveiling the Key Advantages of Digital Twin Technology
Smarter Decision-Making with Real-Time Insights
Digital Twins are taking engineering and manufacturing to the next level as these processes have enormous amounts of data and simulations for real-time tracking giving way to engineers and businesses to make an informed decision based on data. As a result, it enhances accuracy, efficiency, and responsiveness throughout the different areas of engineering
Cost Reduction and Enhanced Operational Efficiency
Digital Twins allow companies to reduce maintenance costs, minimize waste, and improve resource allocation by identifying inefficiencies and anticipating failures before they happen. This results in huge cost reduction and increased productivity.
Fueling Innovation and Accelerating Development
Digital Twin Technology allows businesses to experiment with new designs, analyze different scenarios, and build new products more quickly. It enables faster research and development process, giving organizations a competitive edge in the market.
Driving Sustainability and Environmental Responsibility
Digital Twin Technology is Key to Sustainability Digital Twins aid eco-friendly engineering practices by reducing energy usage, reducing waste, and improving resource management.
Overcoming Challenges in Digital Twin Implementation
Ensuring Data Accuracy and Seamless Integration
Digital Twins does not work without quality data Incorrect or insufficient data can result in nonrefundable simulations and flawed decisions. There are also complications related to the integration of Digital Twins to current systems that need to be considered.
Addressing High Initial Costs and Investment Risks
The upfront cost can be high, but the longer-term return to Digital Twin Technology is significant. [img: Workers keeping a check on work progress through Digital Twins] Businesses should be mindful of return on investment and throw strategic resources behind Digital Twins to make the math work.
Bridging the Skills Gap and Expertise Shortage
Digital Twin Technology adoption requires employees who are skilled in IoT, AI and data analytics. Companies will need to invest in training and upskilling their employees to maximize the potential of the technology.
Tackling Cybersecurity and Privacy Concerns
Since Digital Twins depend on the exchange of real-time data, they are also susceptible to cyber threats. Cybersecurity measures, data encryption, regulatory compliance, and a consistent effort to implement and maintain the necessary infrastructure to keep systems secure are critical to prevent sensitive information from leaking.
The Road Ahead: Future Prospects of Digital Twin Technology
Digital Twin Technology is continuously evolving, fueled by advancements in AI, Machine Learning (ML), and the internet of things (IoT). With the ever-increasing adoption of smart solutions across industries, Digital Twins will become a core enabler of greater efficiency, less risk and increased innovation. As digital twins become established in a range of sectors — from smart cities to autonomous vehicles — the potential applications of Digital Twin Technology will only continue to grow and shape the engineering landscape for many years to come.
From improved product design and testing to enhanced… Digital Twin Technology: Enabling Smarter Business Operations To begin with, this is only the beginning of a more digital and connected world, with Digital Twin technology leading the charge towards this revolution.
Follow Milestone PLM Solutions for Mechanical Industry Updates, CAD Tips and Global Mechanical News.
Milestone PLM Solutions with its exclusive delivery center in India is a global CAD, CAM & FEA services outsourcing partner serving the needs of the Mechanical, Millwork and Automotive industry since 2004. MILESTONE focuses on the unique needs of clients and believes in tackling real-life problems with efficiency, smooth and ease.
The MILESTONE team can assist you with Product Design, 3d Modeling, Drafting & detailing, Reverse Engineering, FEA Analysis and more. We support multiple software including AutoCAD, SolidWorks, Catia, NX, Inventor, Solidedge & Ansys etc. Our approach is to provide a dedicated team for each customer over ongoing project and deliver the quality output consistently.
With our state of art technology and large talent pool of Engineers, we are developing best in class solutions for our customers across the globe. We align with your culture and values to form unbreakable partnerships and are primed for success with over 100 employees and 150 customers in the US, Europe, India, and Asia.
You can email us at info@milestonetech.net and can log in to our website www. milestonetech.net to know more about our services and our work portfolio or contact us on +1-844-598-0005